What is Optical Bonding? A Guide to Industrial Displays
- Daniel Zaichik
- Jul 30, 2023
- 5 min read

What is Optical Bonding?
In display technologies, optical bonding stands out as a fascinating process that brings two optical materials together, not with conventional glue, but through the power of intermolecular forces. Put simply it is when a resin is applied between a touchscreen and a thin-film-transistor liquid-crystal display (TFT LCD) panel.
When investing in screens or displays, opting for optical bonding proves to be a game-changer. This technique dramatically enhances visibility, and boosts the clarity of on-screen content, while also extending product lifespans. Ultimately, improving the overall user experience and the overall value of industrial display systems.

What Is OCR or “Wet Bonding"?
Optically Clear Resin (OCR), also known as "Wet Bonding," is a form of optical bonding that revolutionizes display screen technology. In this process, a clear resin, typically an optical cement, is delicately applied onto the display surface, and additional optical elements like glass covers or touchscreens are precisely adjusted onto the resin layer.
Upon completion, the clear resin is cured, transforming the liquid into a solid form. The result is a seamless integration of the separate optical components, creating a display that boasts unparalleled visual quality and physical durability.
The process involves a two-part system. Firstly, optical cement or resin is carefully mixed in precise ratios and filtered to eliminate any trapped air or debris. Subsequently, the second part consists of curing the optical adhesive, which is achieved through UV curing. Compared to older methods that relied on time or increased temperatures, UV curing significantly reduced curing time to approximately an hour. However, cleanup is essential post-curing, as the process can be somewhat messy.
A popular choice for adhesives in wet optical bonding is silicone, a trusted material that dates back to the 1970s when it was first introduced in LCDs. Silicone's desirability stems from its low thermal expansion rate, low chemical reactivity, low conductivity, water repellency, design flexibility, and its ability to maintain clarity over extended periods—all at an affordable cost.

What is OCA or “Dry Bonding”?
While liquid optical bonding remains popular and widely used, there is always room for improvement. Introducing Optically Clear Adhesive, also known as "dry bonding," a cutting-edge form of optical bonding that takes display technology to new heights. Unlike its liquid counterpart, OCA is a solid material composed of silicone or acrylic, making it a "dry" bonding solution.
OCA comes in the form of a precisely cut dry sheet with a double-sided liner for seamless application. The bonding process involves an initial lamination, followed by pressure applied to the optics within an autoclave. This remarkably efficient process takes less than 30 seconds to complete.
Dry bonding takes place in a clean room environment, free of debris and trapped air, eliminating unnecessary complexities associated with the two-system wet bonding process. The absence of liquid materials streamlines the bonding procedure, ensuring results in less time.
With OCA/dry bonding, display technology achieves significant improvements in clarity, durability, and precision. This innovative approach presents a game-changing solution for various industries seeking optimal performance and reliability in their display systems.

Wet vs Dry Optical Bonding
Wet bonding's two-part system demands meticulous preparation to avoid air bubbles and foreign debris in the resin mixture, requiring expert knowledge from the manufacturer. Moreover, once liquid resin is cured, reworking becomes unfeasible, leading to product wastage and potential damage to the display system during bonding. The longer processing times further add to the complexity of wet bonding.
In contrast, dry bonding offers a streamlined solution with faster processing times, reworkability, and cleaner handling of solid materials. Automation becomes more accessible, and the bonding process benefits from increased shock/vibration and temperature resistance. Notably, the curing of the dry film sheet before bonding eradicates the risk of "yellowing" often observed in resin-based applications.
What about Air Gap Bonding?
Air-gap bonding, also known as framed adhesive, employs a gasket placed around the edges of the display to connect two display optics together, creating an "air gap" between the display screen and the additional optics.
This bonding method stands out for its affordability, as it requires no cure time and readily available materials. Its lightweight nature makes it a popular choice for display technologies that don't demand resistance to volatile environments, such as the outdoors with potential glare issues or exposure to extreme temperatures and high humidity levels that might affect device performance.
Air-gap bonding offers a budget-friendly and practical solution for display applications that don't require the robustness of other optical bonding methods.
How Does Wet Or Dry Optical Bonding Improve Visibility?
In a word: Refraction. Refraction occurs when light rays bend upon passing through different mediums. When multiple layers of mediums are involved, more refraction occurs, leading to readability issues for end-users. Essentially, light reflects off the screen, making it difficult to view the display's content.
In outdoor or harsh conditions, air gap bonding proves insufficient due to higher refraction rates and moisture build-up caused by the gap between the two optics. In these circumstances, wet and dry optical bonding emerges as more viable options, effectively filling the gap between the optical elements. This not only improves the product's environmental performance but also enhances its ruggedness.
By addressing refraction challenges through advanced bonding techniques, display technologies can offer enhanced clarity and readability, ensuring optimal performance in a wide range of environments and conditions.
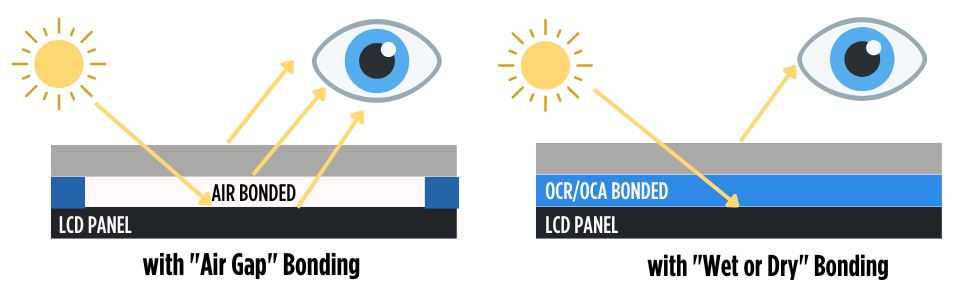
What are the advantages of wet and dry optical bonding?
Utilizing wet and dry optical bonding methods results in significant improvements to the strength and quality of display systems, delivering a host of benefits, such as:
Enhanced Readability in High Sunlight Areas:
Lower reflection ensures visibility, even in brightly lit environments, offering an enhanced display experience.
Elevated Graphic Performance:
Higher contrast, color saturation, and wider viewing angles elevate graphic performance, providing users with more vivid visuals.
Increased Durability and Ruggedness:
Optical bonding provides heightened impact and shock absorption capabilities, protecting displays from accidental damage.
Extended Product Lifecycle:
Through resistance to moisture and condensation, optical bonding prolongs the lifespan of display systems, reducing overall maintenance costs.
Optimal Touchscreen Performance:
The additional resin layer enhances touchscreen responsiveness, maintaining accurate touch responses, and ensuring seamless user experience.
Examples of Optical Bonding Applications Across Industries
Optical bonding, specifically wet and dry bonding, is beneficial for enterprises operating in challenging environments air-bonded display systems would not fare well. Some industries that benefit from optical bonding include:
Food & Beverage:
Frequent washdowns for maintenance of hygiene standards can be handled with ease by optically bonded displays, ensuring uninterrupted operation.
Medical, Healthcare, and Pharmaceutical:
Display systems exposed to liquids and chemicals are protected against corrosion, ensuring reliable performance in critical medical environments.
Outdoor Displays and Digital Signage:
Optimal readability under sunlight or strong headlights ensures users can read screens effortlessly from a distance.
Kiosk Applications and Human-Machine Interface (HMI):
High ruggedization requirements for outdoor vending machines and cashiers are met, reducing downtime due to frequent customer use.
Military, Marine/Offshore, Aviation, Freight, and Logistics:
Resilient against high glare, condensation, and extreme weather changes, optical bonded displays excel in demanding environments with shock and vibration challenges.
Anticipated Trends in Display Technology
As the Industry 4.0 revolution unfolds, automated machines and processes become more prevalent, with computer displays emerging as the primary mode of human-machine interaction. Today, screens are no longer confined to desktops but are integrated into various everyday tools, such as kitchenware, smartwatches, and even vehicles. With increasing screen-time for users, the importance of optical bonding cannot be overstated in enhancing user experience and product longevity.
In the industrial landscape, investing in optical bonding proves to be highly valuable. The impacts of global warming, including brighter and warmer days, unpredictable downpours leading to higher humidity, and even harsher winters, pose challenges for display systems to function seamlessly.
Furthermore, with the exponential rise in data production and daily interactions through these displays, ensuring optimal functionality becomes crucial for promoting data security and protecting personally identifiable or private information for enterprises. The stakes are high, as data-loss and leaks may be just a mis-click away.
In this evolving digital era, optical bonding emerges as a compelling solution to elevate user experience, bolster display performance, and safeguard data integrity for industries at the forefront of technological advancements.
Contact Us for inquiries - optically bonded displays for any environment!
Bình luận